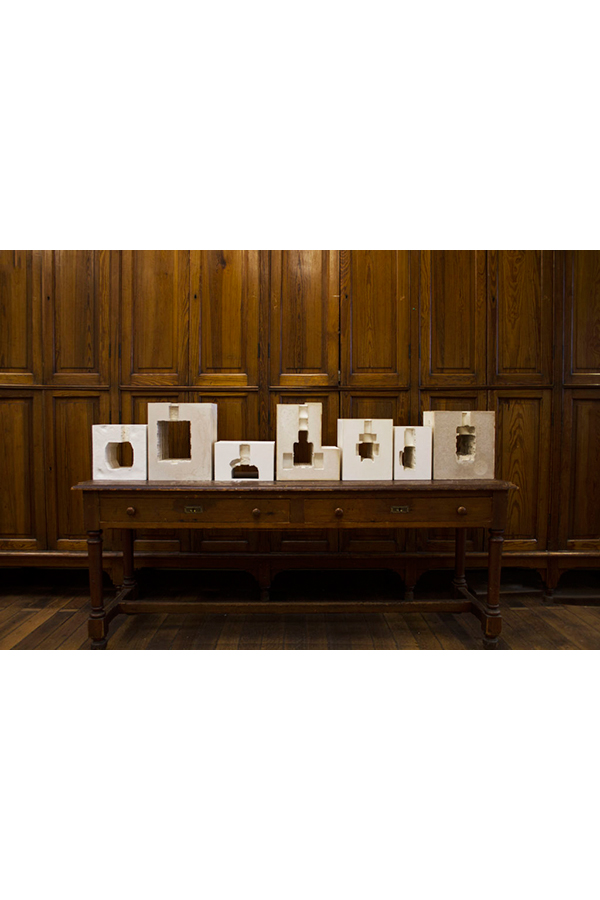
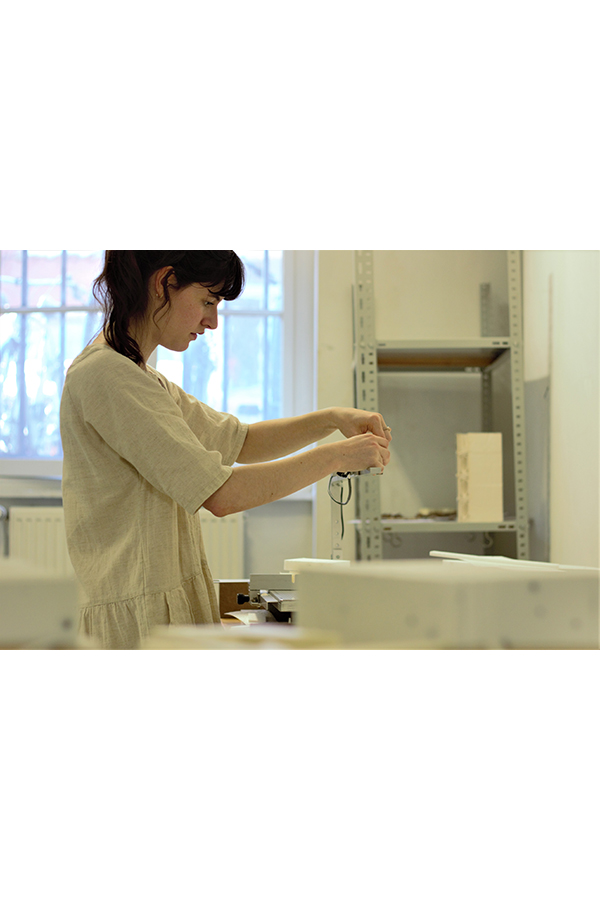
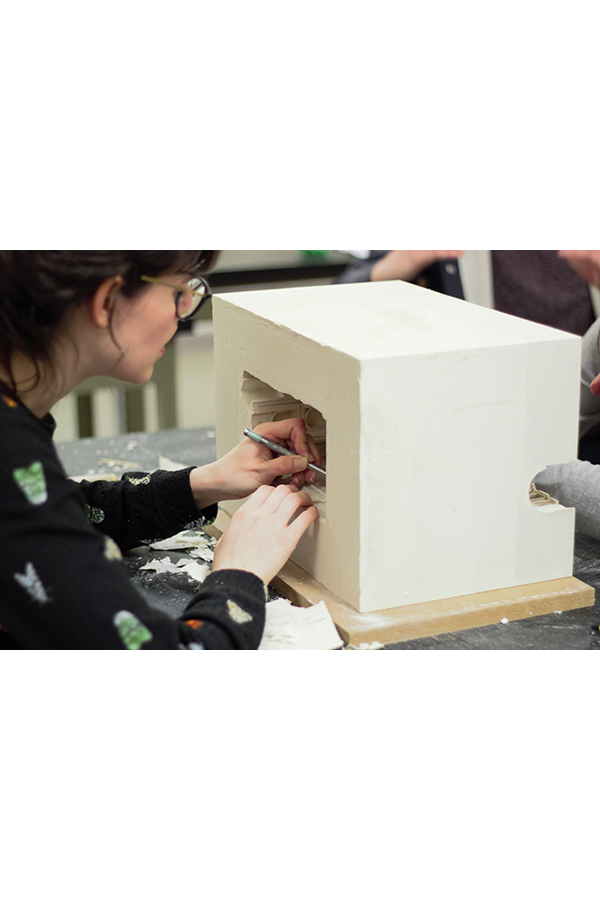
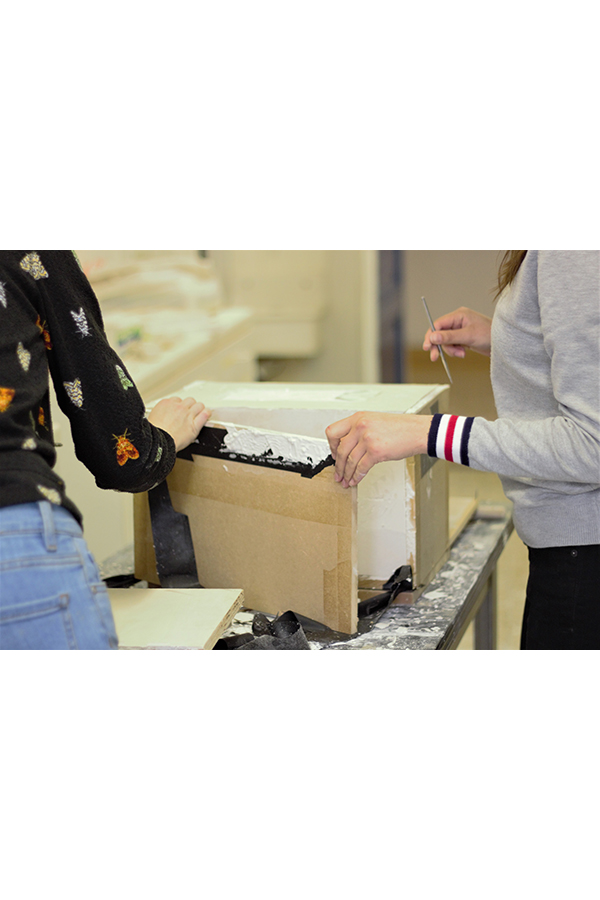
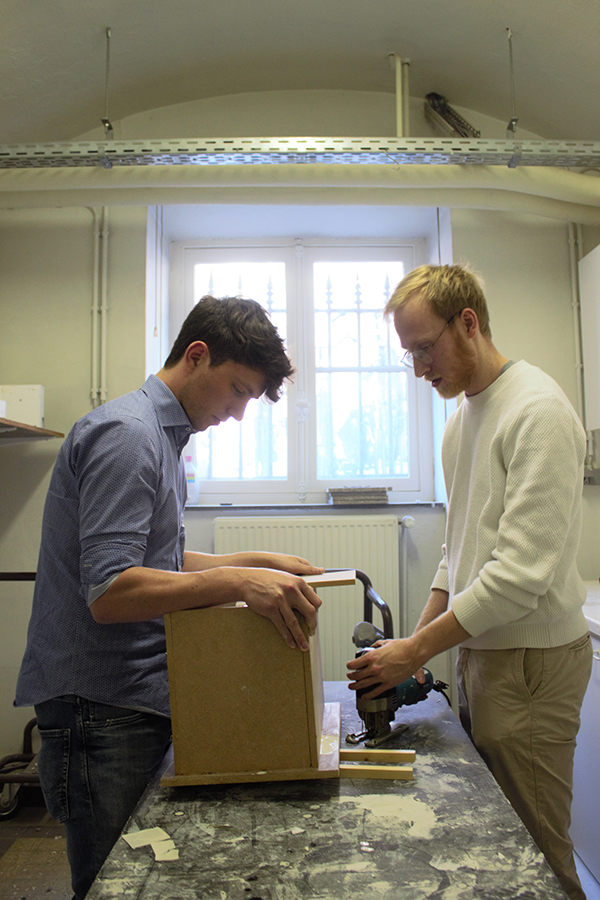
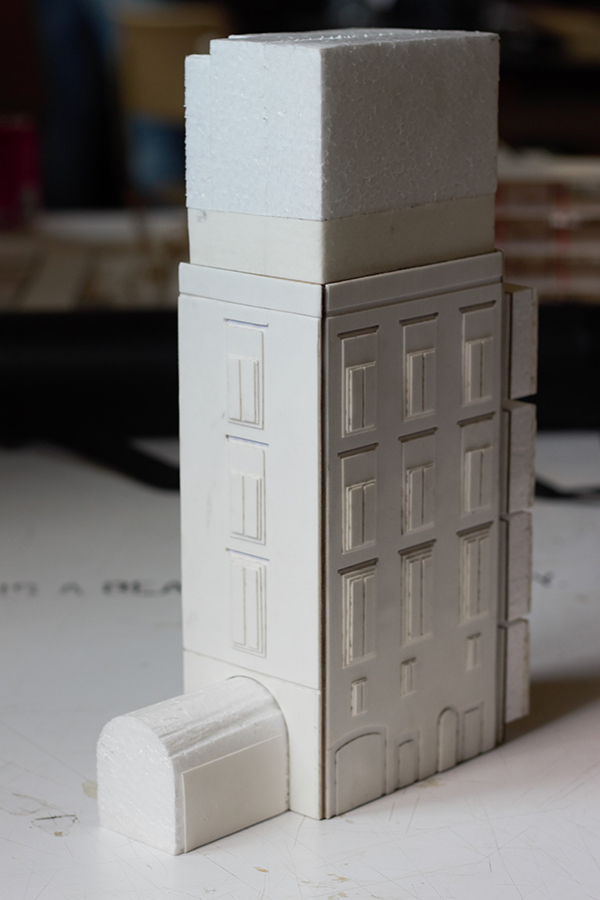
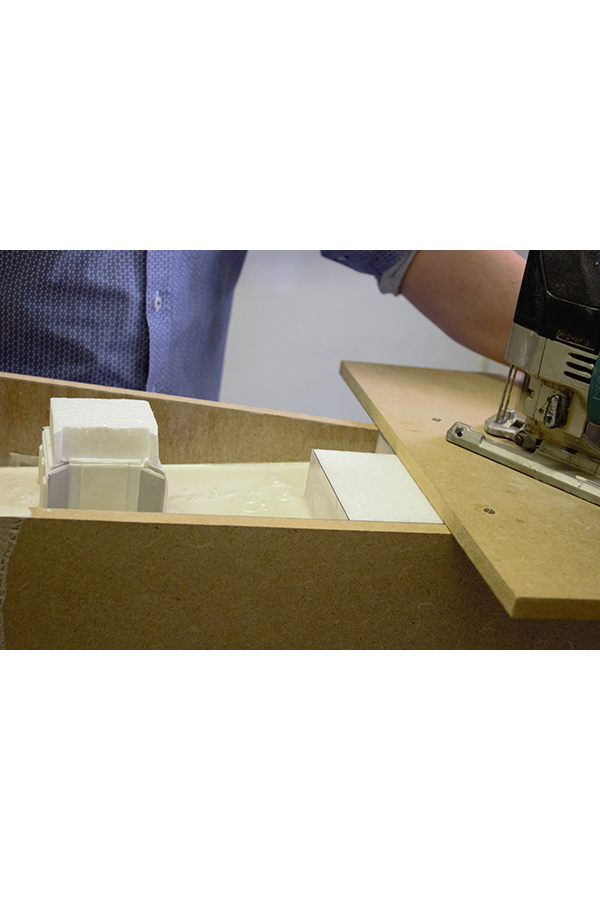
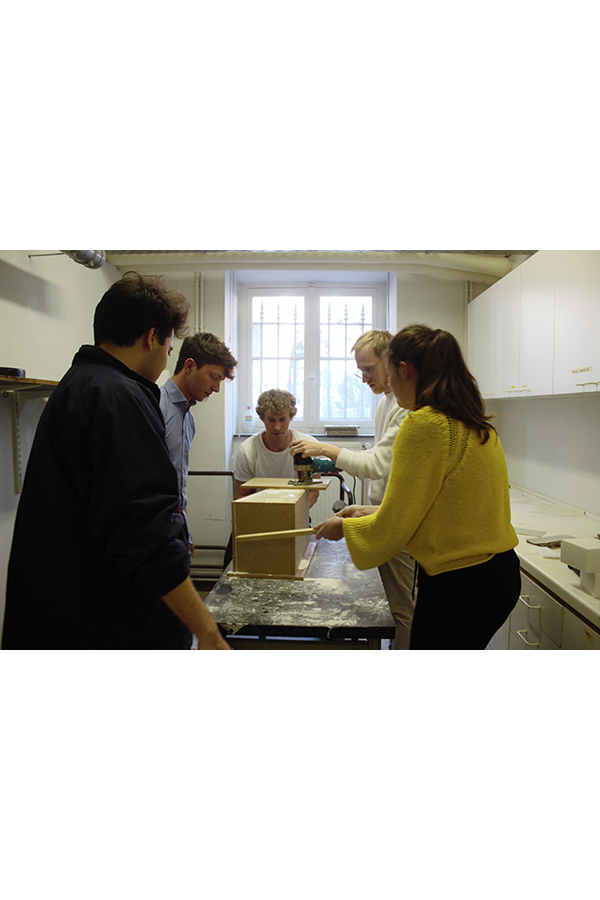
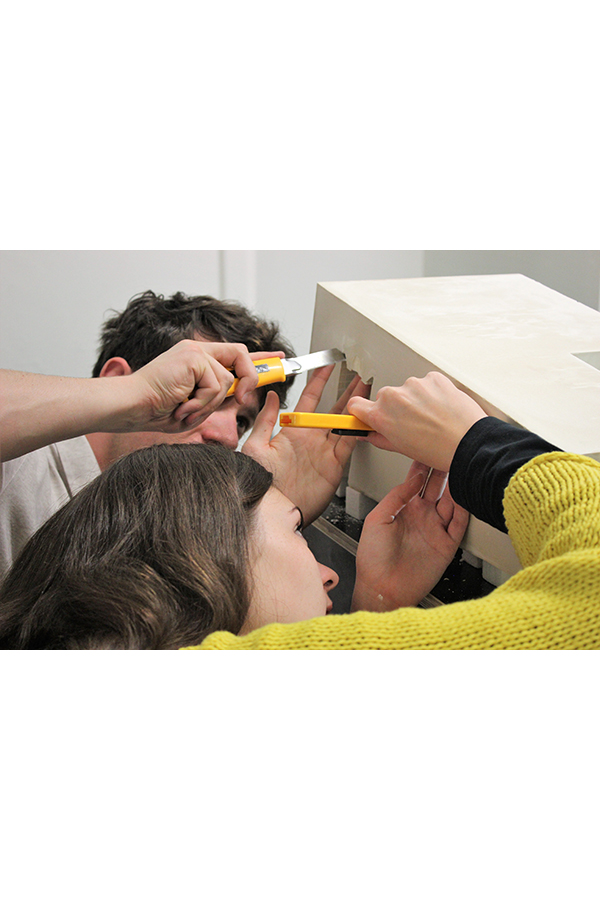
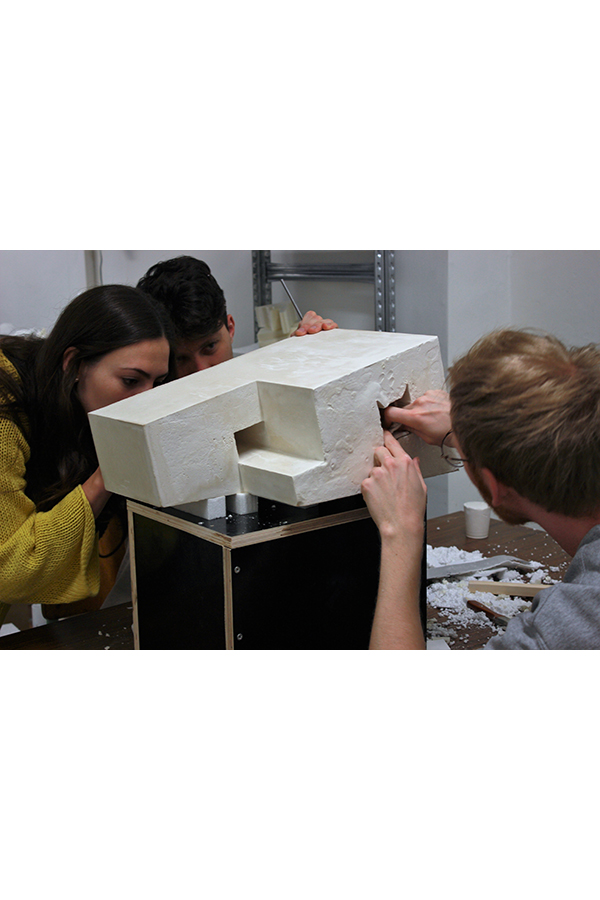
Cast moulding is a modelling technique the popularity of which has grown considerably over the past few years at our university, especially in the master studio of prof. Dirk De Meyer. Contrary to traditional models, cast models focus on the voids it creates, rather than the mass. Hence this material serves both the purpose of this studio and the idea of Naples: a chaotic and hyper dense city in which the voids—the cortile, and their stairs—become of crucial importance.
Like the actual model, the principle of making such a volume is inverted compared to traditional modelling techniques. Since the plaster is poured into the mould, one’s task is to make a negative of the volume. This was realized by combining multiple—more traditional and familiar—modelling materials such as foam, cardboard, wood and vinyl. A big foam block is cut in the shape of the cortile, on which multiple layers of 1mm laser cut foam are glued to accurately represent the tectonics of the facades. Being attentive while drawing the laser cut file is paramount, considering this peculiar way of thinking allows for more mistakes to be made. In the second year of this Master’s seminar, the students opted to pick foam over cardboard (which was used the year before) to construct the cortile’s facades. The former proved to peel off of the plaster way easier during the dismantling of the mould, whilst also allowing more detailing.
Once the void of the cortile is finished, this is attached to the mould. This mould represents the volume of the palazzo, and is mostly constructed in concreteplex, which gives the outside of the cast model a smooth touch and cleaner look. Other students preferred to use other kinds of wood like MDF or multiplex, coated with PVC to achieve the same texture as the aforementioned material. The mould is put together with screws. During this phase, glue is used sparingly. In some rare occasions glue serves as a last resort to fill up little holes in between the different plates to avoid leaking. However this should be done with utmost care, as too much glue can make the dismantling significantly harder.
After completing the mould, the plaster is being prepared. Usually the mould gets to ‘rest’ for a few days to ensure everything dried up completely. To guarantee optimal results, the different batches of plaster should consist out of the same water to plaster ratio. Therefore the usage of a scale is recommended. Also, it is desirable to use a plaster mixture of the same age, so the mixing should be timed. If certain batches are mixed longer than others, it is possible that clumps start to form in the mixture, which can affect the result of the model. During the casting the mould is being vibrated, which enables the air in the mixture to escape out of the liquid. All these parameters turn the casting of the model into a true team-effort. One or two people are needed stir the plaster and time the mixing. When the first bucket has the desired viscosity, one person pours the mixture in the mould, and the second batch is being prepared under the same conditions as the former. The mould is being vibrated by one person as someone else ensures the plaster is spread evenly to avoid big holes in the model. If the model is of a substantial size, it is possible the water pressure will push the cortile out of the mould (this has happened before). Unless if one is looking to mimic the launch of a rocket into outer space, putting some extra reinforcements to keep the cortile in its place won’t do any harm.
When the casting is done, the easiest task of the process—waiting—begins. Technically it is possible to dismantle the mould a few hours after the casting, nonetheless it is safer to let the model dry for a few days. This ensures the model will be completely toughened. After removing the mould, the foam is being removed carefully.
Cast models are—like modelmaking in general—a very work-intensive undertaking. The subtle but impactful differences in the working methods force the students to be very aware during the preparation and buildup. Unlike traditional modelmaking, a mistake can render the mould utterly useless. In most cases, this means the only solution is starting over. However, if no mistakes were made the results are astonishing, which make all the efforts worthwhile.
Aiko Friant